Comprehensive Introduction to Control Cabinet
I. Definition and Function
A control cabinet is an enclosure where switching devices, measuring instruments, protective electrical appliances, and auxiliary equipment are assembled in a closed or semi - closed metal cabinet or on a screen according to electrical wiring requirements. Its layout should meet the normal operation requirements of the power system, be convenient for maintenance, and not endanger the safety of personnel and surrounding equipment. It can centrally control, protect, and monitor electrical equipment and is an indispensable and important device in power systems, industrial automation, and other fields.
II. Classification
By Voltage Level:
It can be divided into low - voltage control cabinets (generally referring to AC 1000V and below) and high - voltage control cabinets (usually referring to AC above 1000V). Low - voltage control cabinets are commonly used in power distribution and equipment control in civil buildings, small factories, etc. High - voltage control cabinets are mainly applied in power substations and high - voltage power supply systems of large - scale industrial enterprises.
By Purpose:
There are
Electrical Control Cabinets, frequency - conversion control cabinets, fire control cabinets, PLC control cabinets, etc.
Electrical Control Cabinets are responsible for the control and power distribution of general electrical equipment. Frequency - conversion control cabinets achieve the speed - regulation operation of motors by adjusting the power frequency of the motors. Fire control cabinets are used to centrally control fire - fighting equipment to ensure fire safety. PLC control cabinets use programmable logic controllers (PLCs) as the core to achieve complex automated control logic.
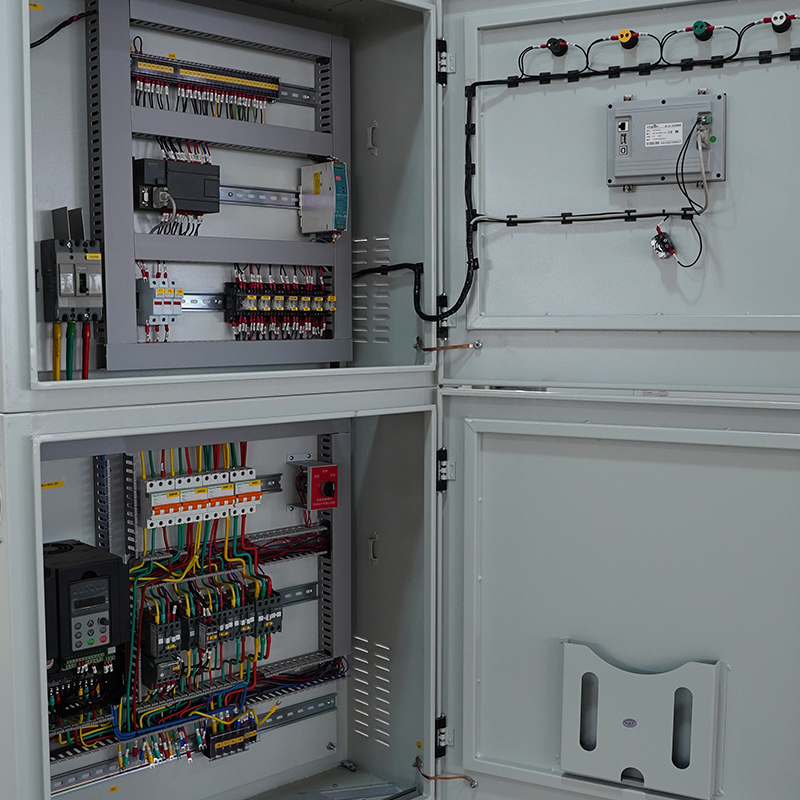
III. Structural Composition
Cabinet Body: Generally made of cold - rolled steel plates, it has good mechanical strength and protective performance. The structural design of the cabinet body needs to consider factors such as ventilation and heat dissipation, dust and moisture prevention, and ease of installation and maintenance. Common cabinet forms include floor - standing type and wall - mounted type.
Electrical Components: Include circuit breakers, contactors, relays, fuses, thermal relays, etc. Circuit breakers are used to cut off the circuit to protect equipment from overload, short - circuit, and other faults. Contactors are used to control the on - off of the circuit to achieve the start - stop control of equipment such as motors. Relays can realize signal conversion and control. Fuses quickly cut off the current in case of overload or short - circuit in the circuit, playing a short - circuit protection role. Thermal relays are used for the overload protection of motors.
Control System: Such as PLCs, single - chip microcomputers, etc. They are the "brains" of the control cabinet. They process input signals through pre - written programs and output control signals to achieve the automated control of equipmen
IV. Working Principle
The working principle of the control cabinet is based on the basic principles of circuits. When the power supply is connected to the control cabinet, the electrical energy is distributed and controlled through the internal electrical components. For example, in motor control, the operator makes the contactor act through the buttons on the control cabinet or remote control signals to connect or disconnect the power supply of the motor, thus realizing operations such as the start, stop, forward and reverse rotation of the motor. At the same time, various protective components continuously monitor parameters such as the current and voltage of the circuit. Once an abnormality is detected, they immediately act to cut off the circuit to protect the safety of equipment and personnel.
V. Application Fields
Industrial Automation:
On the production lines of factories, control cabinets are used to control various mechanical equipment, such as machine tools, conveyors, robots, etc., to achieve automated control of the production process and improve production efficiency and product quality.
Power System:
In power substations, distribution rooms, and other places, control cabinets are used for power distribution, control, and protection to ensure the stable operation of the power system.
Construction Field:
Used for the control of lighting, air - conditioning, water supply and drainage, and other equipment in buildings to achieve intelligent management and improve the energy - use efficiency and comfort of buildings.
Transportation Field:
In the fields of rail transit, ships, etc., control cabinets are used to control power systems, lighting systems, communication systems, etc., to ensure the safe operation of transportation vehicles.
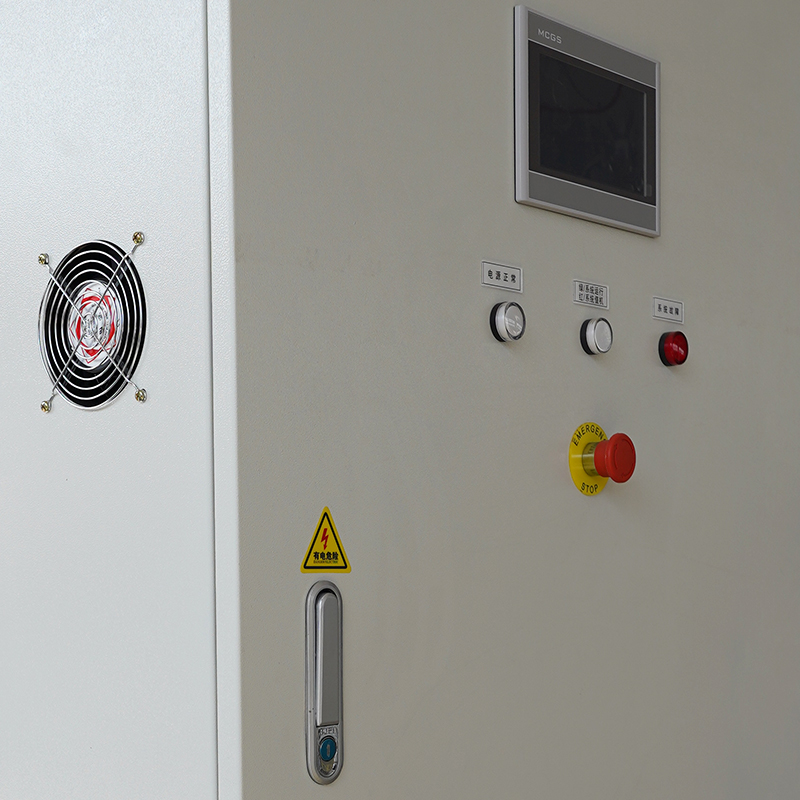
VI. Maintenance and Upkeep
Regular Inspection:
Regularly check the integrity of the cabinet body to see if there is any damage, deformation, etc. Check whether the connections of electrical components are firm and whether there are any looseness, oxidation, etc. Check the operating status of the control system to see if there are any fault alarms.
Cleaning and Maintenance:
Regularly clean the control cabinet to remove dust, debris, etc. inside to prevent electrical failures caused by dust accumulation. Clean tools such as clean brushes and vacuum cleaners can be used.
Replacement of Vulnerable Parts:
According to the service life of electrical components and the actual operating conditions, promptly replace vulnerable parts such as fuses, contactor contacts, relays, etc. to ensure the normal operation of the control cabinet.